Injuries at work are a pain. Literally and also from a managerial perspective. You must report incidents, jump through the loops of the healthcare system, and, if the injury is serious enough, workers must take time off work.
Working in any industrial setting comes with risks and health and safety protocols. Recycling facilities are no exception. Most recycling lines use large processing machinery, conveyor belts, and vehicles. The range of activities from equipment maintenance, quality control, and moving materials all come with their own set of risks and hazards.
As a manager, minimizing injuries in the workplace should be a top priority. Of course, how you manage the health and safety of your employees will depend mainly on your specific setup. However, the following actions should apply to almost every recycling facility.
Stretching Before Shifts
Isn’t stretching something you do before running a marathon or participating in a yoga class? If that’s the paradigm you currently hold, try challenging social norms and instructing employees to stretch before shifts in the factory. It might feel manufactured at first, but once it becomes a habit, it can be a valuable way to reduce long-term issues like carpal tunnel syndrome and back pain. It also helps reduce muscle strains.
Industry workers are generally keen for ways to mix up the day. Stretching at the start of shifts and after breaks gives employees a welcome change and time to reset their mental energy as well as their bodies.
Set up Accessible Feedback Loops
Feedback loops between workers and managers are vital to fixing any holes in a health and safety system. Feedback loops can operate on a range of different mediums. Regular briefing meetings are likely the best time to connect managers with employees and discuss concerns and best safe practices. Online applications for incident reporting are a great tool as well. A report that workers can fill out on a laptop or a device is much more accessible and, therefore, likely to be used than long paper reports.
Clear Induction Procedure
Inductions often feel like necessary nuisances that are best gotten out of the way as quickly as possible. While inductions might drag on at times, they are vital for making health and safety standards clear.
Take Mark, for example, who has recently started work at a rubber recycling plant. Mark is being given a tour of the tire recycling machinery when he reaches into a tire shredding machine to feel how sharp the blades are. Even though the machine is off, this is a major health and safety breach. The senior employee briefing Mark takes this opportunity to explain the rules around the machinery as well as introduce Mark to the culture of safety that the plant prides itself on.
Employees are especially impressionable when they are new. Taking the time to meet fresh employees where they are and to cover both the rules and the culture around safety is a great step towards an incident-free workplace.
Vinyl Graphics
Informative stickers and floor graphics are ideal for drawing boundaries, no-go zones, and keeping equipment organized. Floor graphics can also serve as reminders every time workers enter a space. Some typical graphics might include:
- Appropriate use of personal protective equipment
- Notice to visitors about hazards operations on site
- Exit and entrance signs
- Speed limits
- Keep clear signs
Ventilation
Most health and safety management revolves around mitigating acute injuries such as cuts, bruises, and overloading. Although these types of incidents are important to keep on top of, some of the more sinister health concerns often come from less obvious hazards such as inhaling dust and toxic fumes.
Proper ventilation is especially important in recycling facilities where you heat products, and unknown chemicals might be present in the garbage. Ventilation helps address this issue and decreases the chances of employees spreading common colds and viruses to each other.
Invest in Quality Recycling Equipment
Many incidents in recycling facilities revolve around equipment. Although user error or carelessness is certainly to blame for many incidents, quality equipment can decrease the likelihood of human mistakes.
ECO Green has designed the ECO Brain, which diagnoses issues with tire recycling machinery automatically via a smart computer system. Rather than an employee having to put themselves at risk trying to diagnose the problem. The ECO Brain helps keep the workers away from dangerous equipment as much as possible. This is a prime example of how quality equipment can help keep employees safe.
Although there are many different ways to approach safety, one of the most important things to focus on is cultivating a culture of safety in your workplace. A culture of safety combined with specific actions and protocols ensures that your recycling plant is an environment where workers can do their best work.
Infographic
Recycling facilities are one of the many industries with risks and hazards. Managers should always prioritize minimizing injuries in the workplace because it’s going to be a pain when a worker is seriously injured and needs to take time off work. Establishing a culture of health and safety in the workplace with the following actions can help ensure employees’ safety at all times.
Video
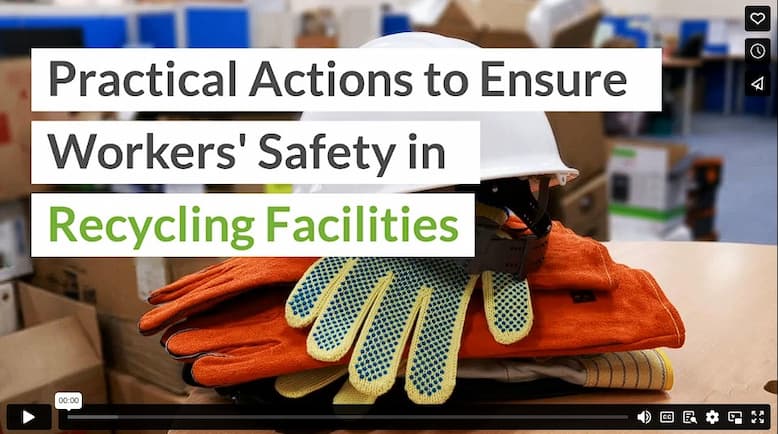